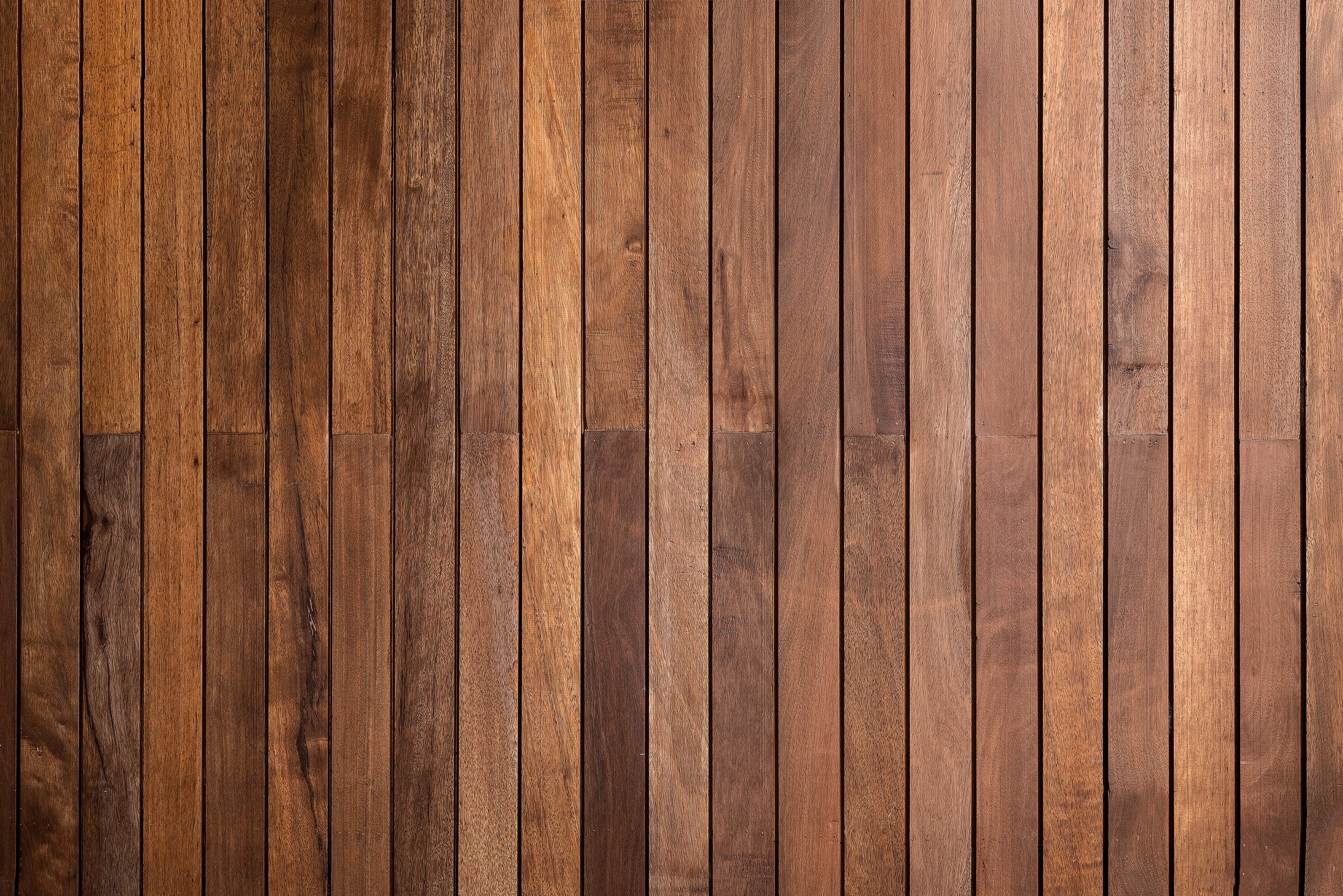
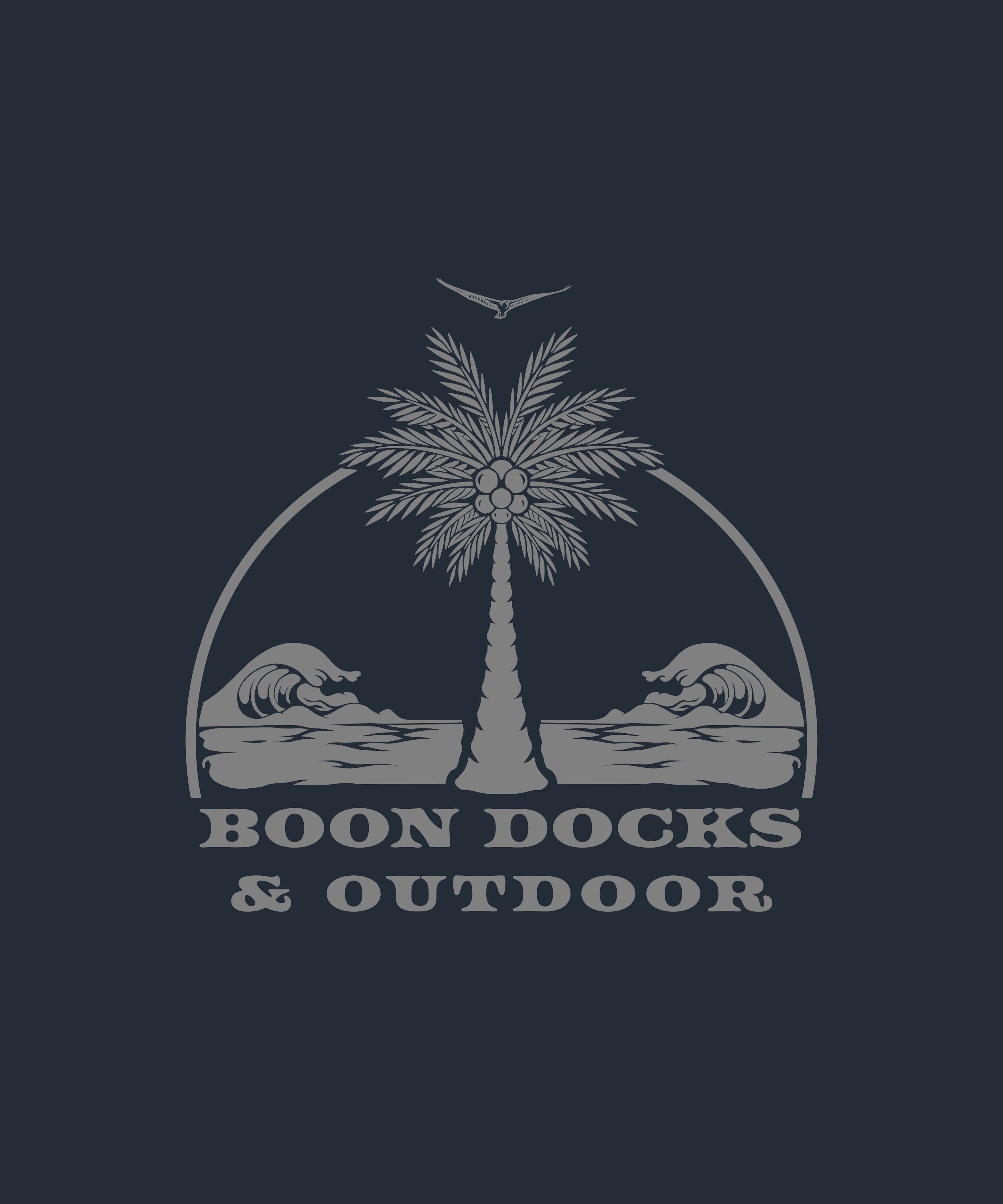
How Much Does a Deck or Boat Dock Cost ?
And other Frequently Asked Questions
-
As you would expect, this answer will vary based on many factors. The bulk of your deck or dock costs will center around materials and labor, of course. From there, larger design decisions like type of railing, boat lift arrangements, and type of roof coverings are some options that will impact the costs, too. Grade of lumber, type of decking, stainless-steel hardware vs. galvanized, hidden fastener systems vs. traditional face screws, and site conditions are some considerations that will influence costs even further. Ultimately, we tell potential deck clients to budget at least $40 per square foot (SF) of deck space. But that said, this number probably wouldn't compute for a small 4'x6' stair landing you need constructed. Your cost per SF will be much greater than $40 per SF. The same idea can be applied to an extremely large deck. It may likely work out to be less than $40 per SF. You get more 'bang for your buck' the larger your deck, so to speak. Docks can be even harder to determine a SF cost for. Their size and design can vary dramatically. But generally speaking, for a classic dock and boathouse like you might find in our gallery, you should be prepared to spend as much as you might for a new car. Figure your average dock costs about $60K. Having said all that, having a discussion about your unique project is extremely important when determining a budget number for your outdoor structure. And if you've read this far, we could have probably already given you a more accurate number with a brief phone call.
-
We prefer to visit the site of the project and meet with you before we prepare a formal design and price quote. We approach each meeting ready to answer whatever questions you have and we'll gladly offer input when asked, and maybe even some code compliance considerations when not. Once we've gathered the various notes and site sketches, it'll take a day or so to prepare a detailed proposal with material and design specifics, scope of work, construction methods, project price complete with various options, payment terms, and all the usual legal jargon you'd find in a professional document. It's not only common, but also encouraged to set up another time to discuss the design details and answer any questions you have gathered after your initial review. Some projects take multiple design revisions before decisions are made. To put it briefly, you send an email or call to schedule a free design consultation and price quote. We discuss. We put together a custom design and email my formal proposal with scope of work and costs detailed. After some possible design tweaks, hopefully a rewarding Q&A session, you say “Yes” to the design, we say “Excellent!”, and we get things moving forward.
-
Most projects start with the permitting process. We handle each phase of permitting, so your biggest responsibility will be signing a few permitting documents. As we begin that process, we'll also be drafting and preparing your engineered stamped plans for the building permit. Depending on the size and scope of your project, the deck and dock permitting phase can take anywhere from 1 to 3+ months. This is usually a fairly quiet time, as far as you're concerned. We'll be working behind the scenes, answering whatever questions the building department may be asking while you patiently wait for your new build to commence. Once the permit has issued, we can confirm a date to start the construction of your outdoor structure. We like to conduct a pre-construction meeting with you before we start, just to answer any remaining questions, and make sure we've dotted all of our "i's" and crossed all of our "t's". We should be able to complete most projects within several weeks. Ultimately, permitting and constructing a new deck or dock can be a process that takes several months to complete. We consider it a short-term relationship so we find the team-based approach extremely conducive to a successful project.
-
YES! Even some minor deck or dock repairs will require a permit. And when it comes to boat docks, seawalls, and even floating docks, we will need to obtain your environmental permit in addition to the standard required building permit. The permit process can be a mundane, frustrating process, but it’s a process we're familiar with and will handle each step along the way. Give us a call if you’d like to discuss your specific scenario in more detail.
-
This used to be an easy question. Years ago, the cheap composite decking simply looked cheap. It looked like a piece of painted plastic compared to the more aesthetically pleasing, multi-chromatic color hues, and realistic grain patters of the more expensive stuff. Nowadays, with the decking market much more competitive, and with so many more options available, the differences go beyond just the look of the product.
Generally speaking…
PVC decking tends to remain a bit COOLER to the touch than the more dense composite decking options. That said, many composite decking manufacturers are now offering specially engineered deck boards that rival the cooler nature of PVC decking.
PVC decking is MORE RESISTANT to moisture, mildew, and mold because it is engineered from 100% synthetic materials. Composite decking contains both synthetic materials and organic wood fibers, making it more prone to mildew and mold growth, particularly during long periods of water exposure.
PVC decking tends to be MORE EXPENSIVE. The engineering processes and the use of all synthetic materials come with the benefits, but with a higher price tag, too.
Composite decking feels a bit MORE RIGID under the feet. The use of wood fibers in the manufacturing process seems to make for a heavier and more dense deck board, which can help sustain the quality of installation throughout the constant expansion and contraction that happens with outdoor building materials, especially PVC.
Both PVC and composite decking options are covered under LENGTHY WARRANTIES. The length of these warranties will vary dependent on which specific type of decking, and from which manufacturer, you choose. Keep in mind, whatever the warranty offered, it will only be honored if the decking material used was installed correctly. This may be one of the more important, and oftentimes overlooked, reasons to hire a professional deck/dock builder that is familiar with these types of installations.
Beyond these general comparisons, there are even more subtle differences between the numerous PVC decking and composite options. Send us an email or give us a call if you’d like to setup a time to meet, discuss, and check out some of the decking samples we offer.
-
At the very least, all wood support pilings will be pressure treated to meet use category UC4B. Although you may hear the term “marine-grade” used often, that term is typically reserved for lumber that is treated to meet use categories UC5A-B-C, or “Continuous marine exposure”, as it relates to saltwater applications. In general, UC4B pressure treated lumber is more common to freshwater lake installations. Have a look at this chart for a more complete look at the use categories.This pic may help visualize, too.
With that, all wood framing lumber will be #2 grade or better. In general, #2 grade framing lumber is used in the construction of your substructure, such as your deck joists, cross-ties, and angle bracing. Since #2 grade lumber may contain more cosmetic defects, it’s more commonly specified in areas of the build that are hidden below deck. DSS (Dense Select Structural) grade lumber is more commonly found in framing members found above the deck level that are more visible, like your roof headers, rafters, fascia boards, and some railing components. However, it’s not uncommon to specify DSS grade lumber throughout each component of the build, including the substructure. It just calls for a slightly higher build budget. Check this link for some info regarding lumber grading.
-
We offer a one year warranty on the integrity of our structural framing, lumber, and the hardware of your structure. If using composite or PVC decking, each manufacturer offers their own product warranties, usually extending at least 25 years. The same can be said for any roof shingles, tiles, or metal panels used in your roof covering. And most of the boat cradle components will be the last pieces that remain when it comes time for potential renovations, decades after the initial structure is built. Be sure to ask about potential maintenance routines and services offered that will keep things fine tuned on a weekly, monthly, or yearly basis. Protect your investment and gain some peace of mind.
DOCKS & BOATHOUSES
DECKS & OUTDOOR
ENGINEERING & PERMITTING
REPAIRS & RENOVATIONS